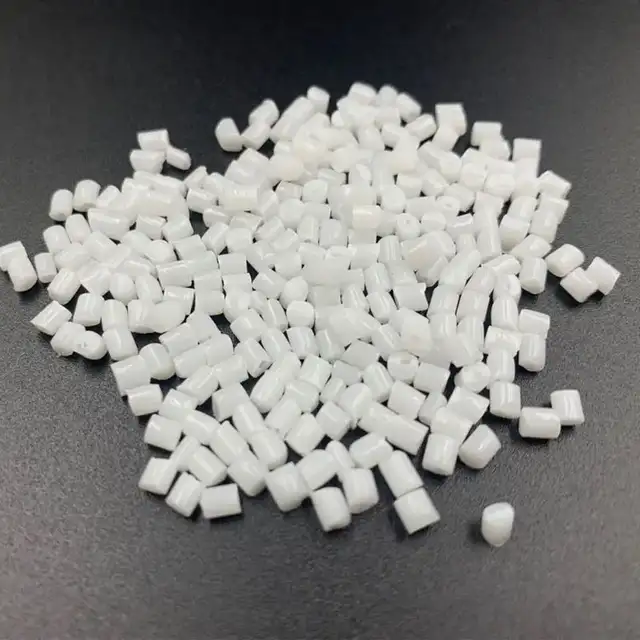
Selecting the right material for custom plastic products is essential for ensuring quality and durability. As a small but dedicated custom plastic and hardware mold factory, we understand the importance of material selection in the injection molding process. This article will cover why material selection is crucial, the types of materials available, and how to choose the best material for your needs.
Importance of Material Selection
The choice of material impacts:
1.Durability: Ensures the product can withstand usage conditions.
2.Cost-Effectiveness: Balances performance with budget constraints.
3.Manufacturability: Affects production efficiency and defect rates.
4.Compliance and Safety: Meets industry standards for safety and recyclability.
Types of Materials
1.Thermoplastics: Common and versatile, including:
2.Polyethylene (PE): Flexible and chemically resistant, used in packaging.
3.Polypropylene (PP): Fatigue-resistant, used in automotive parts.
4.Acrylonitrile Butadiene Styrene (ABS): Tough and impact-resistant, used in electronics.
5.Polystyrene (PS): Clear and rigid, used in food packaging.
6.Polyoxymethylene (POM): High strength, low friction, used in precision parts.
Material | Properties | Common Uses |
Polyethylene (PE) | Flexible, chemically resistant | Packaging |
Polypropylene (PP) | Fatigue-resistant | Automotive parts |
ABS | Tough, impact-resistant | Electronics |
Polystyrene (PS) | Clear, rigid | Food packaging |
Polyoxymethylene (POM) | High strength, low friction | Precision parts |
Nylon (Polyamide) | Strong, wear-resistant | Mechanical parts |
Nylon (Polyamide): Strong, wear-resistant, used in mechanical parts.
Thermosets: Cured permanently, such as:
Epoxy Resins: Strong and resistant, used in coatings and adhesives.
Phenolic Resins: Heat-resistant, used in electrical applications.
Material | Properties | Common Uses |
Epoxy Resins | Strong, resistant | Coatings, adhesives |
Phenolic Resins | Heat-resistant | Electrical applications |
Elastomers: Flexible and resilient, including:
Silicone Rubber: Heat-resistant, used in medical devices and seals.
Thermoplastic Elastomers (TPE): Flexible and durable, used in soft-touch grips.
Material | Properties | Common Uses |
Silicone Rubber | Heat-resistant | Medical devices, seals |
Thermoplastic Elastomers (TPE) | Flexible, durable | Soft-touch grips |
Key Factors in Material Selection
1.Mechanical Properties: Consider strength and flexibility.
2.Environmental Resistance: Assess exposure to chemicals and temperatures.
3.Aesthetic Requirements: Choose based on color and finish needs.
4.Regulatory Compliance: Ensure safety and industry standards.
5.Cost Considerations: Balance performance with cost.
Factor | Considerations |
Mechanical Properties | Strength, flexibility |
Environmental Resistance | Exposure to chemicals, temperatures |
Aesthetic Requirements | Color, finish |
Regulatory Compliance | Safety, industry standards |
Cost Considerations | Performance vs. cost |
Steps to Choosing the Right Material
1.Define Product Requirements: Identify mechanical and environmental needs.
2.Consult Material Data Sheets: Compare properties and performance.
3.Prototype and Test: Evaluate materials in real-world conditions.
4.Evaluate Manufacturing Feasibility: Consider processing and defect potential.
5.Seek Expert Advice: Consult with material and injection molding experts.
Common Challenges and Solutions
1.Balancing Performance and Cost: Conduct a cost-benefit analysis.
2.Material Availability: Build relationships with multiple suppliers.
3.Design Constraints: Optimize design for manufacturability.
4.Environmental Impact: Explore eco-friendly materials like bioplastics.
Future Trends in Material Selection
1.Sustainable Materials: Development of biodegradable and recyclable plastics is reducing environmental impact.
2.Advanced Composites: Innovations in composites, combining plastics with fibers or nanoparticles, enhance properties like strength and thermal stability.
3.Smart Materials: Emerging materials that respond to environmental changes offer properties like self-healing and shape memory.
4.Digital Tools and AI: Digital tools and AI are increasingly used in material selection, allowing precise simulations and optimizations, reducing trial and error.
Selecting the appropriate material for custom plastic products is crucial for ensuring their quality and durability. By thoroughly understanding various materials and carefully evaluating your product's requirements, you can make informed decisions that effectively balance performance and cost. Keeping abreast of new materials and technological advancements will help maintain a competitive edge in the market.