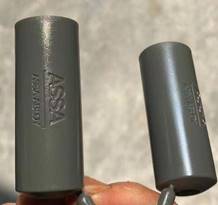
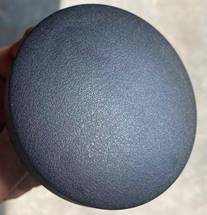
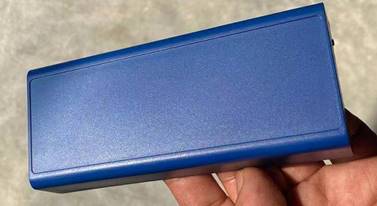
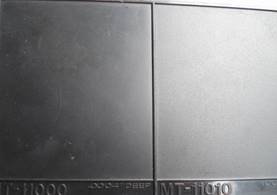
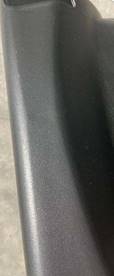
Controlling surface finish in injection molding is crucial for achieving both functional and aesthetic outcomes. A well-chosen surface finish enhances the look and feel of a product, increasing its perceived value and quality. It also impacts the performance and durability of molded parts by improving fatigue strength and minimizing stress concentrations. Different finishes, such as glossy or matte, can produce various visual effects, influencing the product's appeal and usability. By selecting the appropriate surface finish, you ensure that your product not only looks good but also performs optimally in its intended application.
Types of Injection Molding Finishes
Choosing the right surface finish in injection molding is like selecting the perfect frame for a painting. It enhances the product's appearance and functionality, ensuring it meets both aesthetic and practical standards. Let's explore the different types of finishes you can choose from.
Glossy Finish
Characteristics and Applications
A glossy finish provides a shiny, reflective surface that catches the eye. This type of finish is often used in consumer electronics, automotive parts, and household items where a sleek, polished look is desired. The smooth surface can make colors appear more vibrant and details more pronounced.
Advantages and Disadvantages
Advantages:
- Enhances visual appeal with a high-gloss shine.
- Easy to clean due to its smooth surface.
- Can highlight intricate details and designs.
Disadvantages:
- Prone to showing fingerprints and smudges.
- May reveal surface imperfections more easily.
- Requires careful handling to maintain its appearance.
Matte Finish
Characteristics and Applications
A matte finish offers a non-reflective, subdued appearance. It is commonly used in products where a sophisticated, understated look is preferred, such as in certain automotive interiors, consumer electronics, and industrial equipment. This finish can help reduce glare and provide a more tactile feel.
Advantages and Disadvantages
Advantages:
- Hides fingerprints and smudges effectively.
- Provides a soft, elegant look.
- Reduces glare, making it ideal for screens and displays.
Disadvantages:
- Can be more challenging to clean than glossy surfaces.
- May not highlight colors and details as vividly.
- Surface texture might wear over time with frequent use.
Textured Finish
Characteristics and Applications
Textured finishes add depth and complexity to a product's surface. They are often used in applications where grip and handling are important, such as in tool handles, outdoor equipment, and certain automotive parts. Textures can range from subtle patterns to more pronounced designs.
Advantages and Disadvantages
Advantages:
- Improves grip and handling.
- Masks surface imperfections effectively.
- Adds a unique aesthetic element to the product.
Disadvantages:
- Can be more difficult to clean due to grooves and patterns.
- May require specialized tooling and processes.
- Surface texture might wear unevenly over time.
By understanding these finishes, you can make informed decisions that align with your product's goals and customer expectations. Each finish offers distinct benefits and challenges, so consider your specific needs when selecting the right one for your injection molding project.
Factors Affecting Surface Finish
Understanding the factors that influence surface finish in injection molding is crucial for achieving the desired quality and appearance of your products. Let's delve into the key elements that play a significant role in determining the surface finish.
Material Choice
Impact of Different Materials on Finish
The material you choose for injection molding significantly impacts the surface finish of the final product. Different materials possess unique properties that affect how they interact with the mold. For instance, thermoplastics like ABS and polycarbonate often yield a smoother finish due to their inherent flow characteristics. On the other hand, materials with fillers or reinforcements might result in a rougher texture. Selecting the right material is essential to achieve the desired finish and meet both aesthetic and functional requirements.
Material Properties to Consider
When selecting materials, consider properties such as viscosity, shrinkage, and thermal conductivity. These factors influence how the material fills the mold and cools, ultimately affecting the surface finish. High-viscosity materials may not flow as smoothly, leading to potential surface imperfections. Additionally, materials with low shrinkage rates tend to maintain a more consistent finish. By understanding these properties, you can make informed decisions that align with your product goals.
Mold Design
Influence of Mold Texture and Quality
The design and quality of the mold play a pivotal role in determining the surface finish of injection-molded parts. A well-designed mold with a smooth surface can produce a high-quality finish. Mold texture directly transfers to the molded part, so any imperfections in the mold will be reflected in the final product. Using high-quality materials for mold construction, such as hardened steel, ensures durability and precision, which are essential for achieving a glossy finish.
Design Considerations for Optimal Finish
To achieve an optimal surface finish, consider incorporating features like draft angles and uniform wall thickness in your mold design. Draft angles facilitate easy ejection of the part, reducing the risk of surface defects. Uniform wall thickness helps maintain consistent cooling rates, minimizing warping and surface irregularities. By focusing on these design aspects, you can enhance the overall quality of the surface finish.
Injection Velocity and Pressure
Effects on Surface Texture
Injection velocity and pressure are critical parameters that influence the surface texture of molded parts. High injection speeds can lead to a smoother finish by ensuring rapid filling of the mold, reducing the likelihood of flow lines and weld marks. However, excessive speed may cause defects like flash or burn marks. Similarly, maintaining optimal pressure levels helps achieve a uniform surface by ensuring complete mold filling and proper packing of the material.
Balancing Speed and Quality
Balancing injection speed and pressure is essential to achieve the desired surface finish without compromising quality. You should carefully adjust these parameters based on the material and mold design to prevent defects and ensure a consistent finish. Conducting thorough testing and collaborating with experienced injection molders can help you find the right balance, resulting in high-quality, aesthetically pleasing products.
By considering these factors, you can effectively control the surface finish in injection molding, ensuring that your products meet both aesthetic and functional standards.
Temperature Control
Role of Temperature in Surface Finish
Temperature plays a crucial role in determining the surface finish of molded parts. When you control the temperature during the molding process, you directly influence the material's flow and cooling behavior. A consistent and optimal temperature ensures that the material fills the mold evenly, reducing the risk of defects such as flow lines or sink marks. High temperatures can enhance the surface quality by allowing the material to flow more smoothly, resulting in a finer finish. However, excessive heat might lead to issues like warping or degradation of the material. Therefore, maintaining the right temperature balance is essential for achieving a high-quality surface finish.
Techniques for Temperature Management
To manage temperature effectively, you can employ several techniques:
-
Mold Temperature Control Units (TCUs): These devices regulate the mold's temperature by circulating a heat transfer fluid through channels in the mold. By maintaining a consistent mold temperature, TCUs help achieve uniform cooling and prevent surface defects.
-
Heaters and Coolers: Using heaters and coolers strategically can help maintain the desired temperature range. Heaters ensure that the material remains at the right viscosity for smooth flow, while coolers facilitate rapid solidification to preserve the surface finish.
-
Thermal Imaging: Implementing thermal imaging technology allows you to monitor temperature distribution across the mold surface. This technique helps identify hot spots or areas with uneven cooling, enabling you to make necessary adjustments for a consistent finish.
-
Material Selection: Choosing materials with suitable thermal properties can aid in temperature management. Materials with high thermal conductivity distribute heat more evenly, reducing the risk of surface imperfections.
By employing these techniques, you can effectively control the temperature during the molding process, ensuring that your products meet both aesthetic and functional standards.
Reasons for Different Finishes
Surface finishes in injection molding serve various purposes, both functional and aesthetic. Understanding these reasons helps you make informed decisions that align with your product's goals and customer expectations.
Functional Considerations
Durability and Wear Resistance
Surface finish plays a crucial role in enhancing the durability and wear resistance of molded parts. A well-chosen finish can protect the surface from scratches, abrasions, and other forms of wear. For instance, a textured finish can distribute stress more evenly across the surface, reducing the likelihood of damage over time. This is particularly important in applications where parts are subject to frequent handling or harsh environments. By selecting a finish that enhances durability, you ensure that your products maintain their integrity and functionality throughout their lifespan.
Grip and Handling
The surface finish also affects the grip and handling of a product. Textured finishes, for example, provide a tactile surface that improves grip, making them ideal for tools, handles, and other items that require secure handling. This functional aspect is essential in industries such as automotive and consumer electronics, where user safety and comfort are paramount. By choosing a finish that enhances grip, you improve the usability and safety of your products.
Aesthetic Considerations
Visual Appeal and Branding
Aesthetic considerations often drive the choice of surface finish in injection molding. The finish can significantly impact the visual appeal of a product, influencing how it is perceived by consumers. A glossy finish, for example, can create a sleek and modern look, enhancing the product's attractiveness. This is particularly important in consumer-facing industries where branding and visual identity play a crucial role. By selecting a finish that aligns with your brand's image, you can create a cohesive and appealing product line.
Market Preferences and Trends
Market preferences and trends also influence the choice of surface finish. Consumer tastes can vary widely, and staying attuned to these trends ensures that your products remain relevant and competitive. For instance, matte finishes have gained popularity in recent years due to their understated elegance and ability to hide fingerprints. By understanding and adapting to market trends, you can tailor your products to meet consumer demands and preferences.
In conclusion, the choice of surface finish in injection molding is a strategic decision that impacts both the functionality and aesthetics of your products. By considering factors such as durability, grip, visual appeal, and market trends, you can select a finish that enhances your product's performance and aligns with your brand's goals.
To control surface finish in Injection Molding, focus on several key aspects. First, choose the right finish type—glossy, matte, or textured—based on your product's needs. Each finish offers unique benefits, such as a high gloss for visual appeal or a matte finish to hide imperfections. Next, consider factors like material choice, mold design, and temperature control. These elements significantly impact the final appearance and functionality of your product. Finally, consult with experts and conduct thorough testing to ensure your surface finish aligns with your product goals and customer expectations.