Table of Contents
1.Introduction
2.What is Injection Molding?
3.How Injection Molding Reduces Costs
Lower Material Waste
Reduced Labor Costs
Faster Production
Economies of Scale
4.Efficiency Gains with Injection Molding
Streamlined Production
Consistent, High-Quality Output
5.Case Study: Application in Automotive Parts Manufacturing
6.How to Choose the Right Injection Molding Partner
7.Why Choose Ningbo Tiehou Auto Parts for Injection Molding?
8.Conclusion
9.Get a Free Quote
Introduction
As manufacturers face increasing pressure to reduce costs and improve operational efficiency, finding the right production processes becomes more critical. One of the most effective methods for achieving these goals is injection molding. This process not only streamlines production but also delivers high-quality components at a lower cost.
In this blog, we will explore how injection molding can significantly reduce manufacturing costs and improve efficiency, ensuring your company stays competitive in today’s market.
What is Injection Molding?
Injection molding is a manufacturing process where materials like plastics or rubber are heated and injected into a custom mold. The material is then cooled, solidified, and removed from the mold, forming the final product.
This method is known for producing large quantities of identical parts quickly and consistently, making it ideal for mass production across industries such as automotive, consumer products, construction, and electronics.
How Injection Molding Reduces Costs
Lower Material Waste
One of the key benefits of injection molding is its efficiency in material usage. Since the process is highly precise, it uses exactly the amount of material needed to form each part. This significantly reduces material waste, ensuring you’re only paying for the resources you truly need.
Pro Tip: Any excess material can often be recycled and reused, further reducing costs.
Reduced Labor Costs:
Injection molding is an automated process. Once the molds are designed and the machines are set, the process requires minimal human intervention. This reduces the need for skilled labor, saving your company on operational costs.
By using injection molding, you can be sure that your labor expenses will be minimized, especially as your production volume increases.
Faster Production
Speed is another advantage. Injection molding machines can produce thousands of parts in a short period, which helps meet tight production deadlines without compromising quality. Faster production speeds reduce your overhead costs and help you get products to market faster.
Make sure that your production schedules stay on track by utilizing this highly efficient manufacturing method.
Economies of Scale
The more you produce using injection molding, the lower your per-unit costs become. Once the initial mold is created, it can be used repeatedly, leading to significant cost savings as production scales. This makes injection molding an excellent choice for high-volume production.
By leveraging economies of scale, you can be sure that your overall costs will decrease as you ramp up production.
Efficiency Gains with Injection Molding
Streamlined Production
Injection molding eliminates the need for multiple production steps. From design to finished product, the process is simplified, reducing the time and resources needed to manufacture each part. This means fewer delays and more efficient use of your factory’s resources.
Pro Tip: Injection molding can be combined with secondary processes like overmolding to further enhance efficiency.
Consistent, High-Quality Output:
One of the standout benefits of injection molding is its consistency. Every part produced is identical, ensuring you maintain strict quality standards. This reduces the risk of defective parts, which can be costly to correct.
You can be sure that each part will meet your specifications, helping you avoid costly quality control issues.
Case Study: Application in Automotive Parts Manufacturing
Company Profile: A mid-sized automotive parts supplier that produces components for various vehicle manufacturers, focusing on interior and under-the-hood plastic and rubber parts.
Challenge: The company was dealing with increasing production costs and inefficiencies in their existing manufacturing process. They were sourcing parts from multiple suppliers, leading to inconsistent quality and delays in meeting deadlines. Additionally, manual assembly and material waste were driving up costs, putting pressure on their margins.
Solution: The company approached Ningbo Teko Auto Parts Co., Ltd. to transition to a more streamlined production process using injection molding. The goal was to reduce costs, improve production speed, and ensure consistent part quality.
Results:
•15% cost reduction: By switching to injection molding, the company was able to cut material waste and labor costs. The automation of the process led to more efficient production and minimized the need for manual assembly, resulting in a noticeable reduction in overall expenses.
•30% increase in production speed: Injection molding allowed the company to produce parts faster and more consistently, enabling them to meet tight deadlines and increase output without compromising quality.
•Improved part consistency: The custom molds provided by Ningbo Teko Auto Parts ensured that each part met the company's exact specifications, improving product reliability and reducing the rejection rate by 20%.
•Simplified supply chain: By relying on a single, reliable supplier for their injection molding needs, the company was able to streamline their supply chain, reducing delays and ensuring timely delivery of components.
Outcome: The partnership with Ningbo Teko Auto Parts helped the automotive parts supplier achieve a 15% reduction in overall production costs and a 30% improvement in production speed. These gains allowed the company to be more competitive in the market, meet customer demands more effectively, and reinvest the savings into expanding their product line.
How to Choose the Right Injection Molding Partner
When selecting a partner for your injection molding needs, here are a few key factors to consider:
•Experience in Your Industry: Make sure the partner has expertise in your field, such as automotive, consumer goods, or electronics.
•Material Versatility: Your partner should offer a range of materials to match your product's specific needs, from plastics to rubber and metal.
•Scalability: Choose a partner that can easily scale production as your business grows.
•Quality Assurance: Ensure your partner has strict quality control measures in place to avoid delays and defects.
Why Choose Ningbo Teko Auto Parts for Injection Molding?
At Ningbo Teko Auto Parts Co., Ltd., we specialize in providing custom molds and high-quality parts that align with your manufacturing goals. Here’s why you should partner with us:
•Versatile Materials: We work with a wide range of materials, including plastics, rubber, and metal, to meet your exact product specifications.
•Cost-Effective Production: With our streamlined processes and automated systems, we help you reduce costs and boost efficiency.
•Scalability: Whether you need a small production run or millions of parts, we have the capacity to deliver on time, every time.
•Reliable Quality: Our commitment to quality ensures that every part meets your standards, with rigorous quality checks throughout the process.
Make sure that your manufacturing process is optimized for cost and efficiency by choosing Ningbo Tiehou Auto Parts as your injection molding partner.
Conclusion
Injection molding offers unparalleled benefits in terms of reducing manufacturing costs and improving efficiency. From minimizing material waste to speeding up production, this process helps you achieve the best results with fewer resources.
By choosing the right partner, you can be sure that your company will stay competitive in today’s fast-paced market.
Get a Free Quote
Ready to streamline your production and cut costs? Contact Ningbo Teko Auto Parts Co., Ltd. today for a free consultation and quote. Let’s discuss how our injection molding services can help you reduce costs and improve efficiency in your manufacturing process.
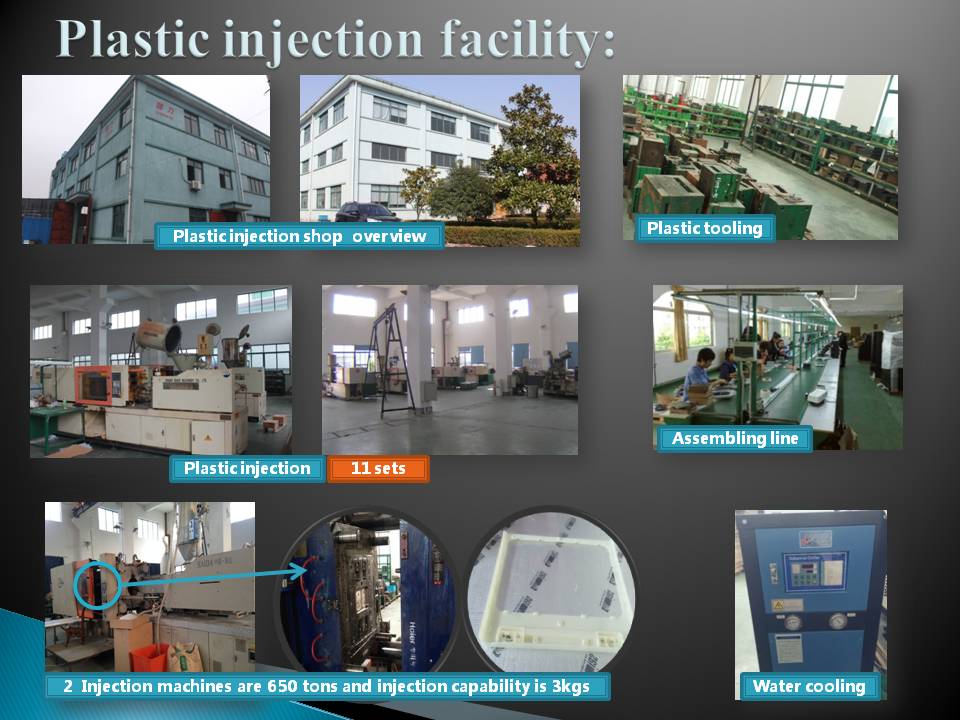