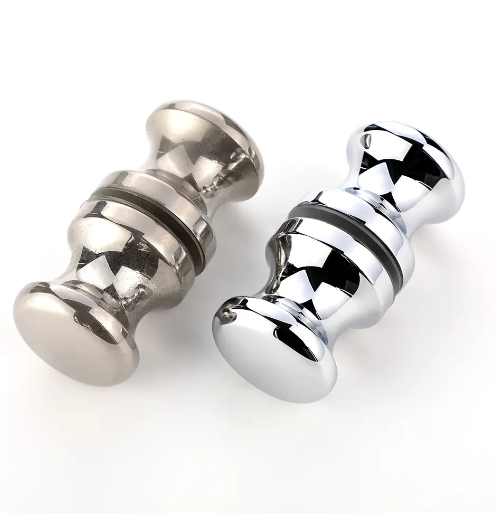
Material Innovations in Door Pull Injection Molding
In the realm of Door Pull Injection Molding, material innovations are paving the way for enhanced product performance and sustainability. As you explore these advancements, you’ll discover how they can transform manufacturing processes and outcomes.
Advanced Polymers
Benefits of using advanced polymers in door pull manufacturing
Advanced polymers have revolutionized the manufacturing of door pulls. These materials offer several benefits that enhance both the production process and the final product. First, advanced polymers provide exceptional strength and durability, ensuring that door pulls withstand daily wear and tear. They also offer lightweight properties, which contribute to easier handling and installation. Moreover, these polymers can resist heat and chemicals, making them ideal for various environments.
Scientific Research Findings:
- High-performance plastics like PEEK and PEI are expanding design possibilities, enabling the creation of lightweight and durable components across industries such as aerospace and electronics.
By incorporating advanced polymers, you can achieve a balance between functionality and aesthetics, meeting the diverse needs of consumers.
Case studies of companies adopting new materials
Several companies have successfully integrated advanced polymers into their door pull manufacturing processes. For instance, a leading automotive manufacturer adopted high-performance polymers to produce lightweight door components. This change not only improved fuel efficiency but also reduced emissions, aligning with environmental goals.
Another example is a company in the electronics sector that utilized advanced polymers to create durable and heat-resistant door pulls for high-temperature applications. These case studies highlight the versatility and effectiveness of advanced polymers in enhancing product quality and sustainability.
Composite Materials
Advantages of composites over traditional materials
Composite materials offer distinct advantages over traditional materials in door pull manufacturing. They combine different substances to create a material with superior properties. Composites are known for their high strength-to-weight ratio, which makes them ideal for applications requiring robust yet lightweight components. Additionally, they provide excellent resistance to corrosion and wear, extending the lifespan of door pulls.
Scientific Research Findings:
- Research on advanced polymer wood composites has shown promising applications in structural members, windows, and doors, emphasizing their potential in construction products.
By choosing composites, you can enhance the performance and longevity of door pulls while reducing maintenance costs.
Examples of innovative composite applications
Innovative applications of composite materials are emerging across various industries. In the construction sector, companies are using flax fibers and composites to develop eco-friendly and durable door components. These materials not only offer environmental benefits but also provide unique aesthetic qualities.
In the automotive industry, composites are being used to manufacture lightweight door panels that improve vehicle efficiency. These examples demonstrate the versatility of composites and their ability to meet modern manufacturing demands.
Technological Advancements in Door Pull Injection Molding
In the dynamic field of Door Pull Injection Molding, technological advancements are reshaping how you approach design and production. These innovations not only enhance efficiency but also open up new possibilities for creativity and customization.
3D Printing Integration
How 3D printing is revolutionizing prototyping and production
3D printing has emerged as a game-changer in the prototyping and production of door pulls. This technology allows you to create complex designs with precision and speed. By using 3D printing, you can quickly produce prototypes, test them, and make necessary adjustments without the lengthy delays associated with traditional methods. This rapid prototyping accelerates the development process, enabling you to bring products to market faster.
Scientists from The Hasso-Plattner-Institut have incorporated metamaterial mechanisms into 3D printing technology, creating innovative solutions like a 3D printed door handle and latch system.
This integration of 3D printing not only streamlines production but also reduces material waste, making it a more sustainable option for manufacturers.
Real-world examples of 3D printing in door pull design
Real-world applications of 3D printing in door pull design demonstrate its transformative impact. For instance, some companies have used 3D printing to produce customized door pulls that cater to specific consumer preferences. This customization allows you to offer unique designs that stand out in the market.
Additionally, 3D printing enables the creation of intricate patterns and textures that were previously difficult to achieve. These advancements provide you with the tools to innovate and differentiate your products, meeting the evolving demands of consumers.
Smart Manufacturing Technologies
The role of IoT and AI in enhancing production efficiency
The integration of IoT and AI in manufacturing processes is revolutionizing Door Pull Injection Molding. IoT devices collect real-time data from production lines, allowing you to monitor and optimize operations continuously. This data-driven approach helps you identify inefficiencies and implement improvements swiftly.
AI algorithms analyze this data to predict maintenance needs and prevent downtime. By leveraging AI, you can enhance production efficiency, reduce costs, and improve product quality. These technologies empower you to make informed decisions and stay competitive in a rapidly changing industry.
Case studies of smart technology implementation
Several companies have successfully implemented smart manufacturing technologies in their operations. For example, a leading manufacturer used IoT sensors to monitor machine performance and detect anomalies. This proactive approach reduced equipment failures and increased production uptime.
Another company integrated AI-driven analytics to optimize their injection molding process. This resulted in significant cost savings and improved product consistency. These case studies highlight the tangible benefits of adopting smart technologies, encouraging you to explore these innovations for your manufacturing needs.
Design Flexibility in Door Pull Injection Molding
In the world of Door Pull Injection Molding, design flexibility has become a significant trend. This flexibility allows you to create products that not only meet functional requirements but also cater to aesthetic preferences.
Customization Trends
Increasing demand for personalized door pull designs
Consumers today seek products that reflect their personal style. This trend is evident in the growing demand for personalized door pull designs. You can offer unique and tailored options that resonate with individual tastes. Personalized designs allow you to stand out in a competitive market by providing something distinct and memorable.
Tools and technologies enabling customization
To meet the demand for customization, you can leverage various tools and technologies. Advanced software enables you to design intricate patterns and shapes with precision. These tools allow you to experiment with different styles and materials, ensuring that each product aligns with consumer preferences. By utilizing these technologies, you can efficiently produce customized door pulls that satisfy diverse customer needs.
Aesthetic Innovations
New design trends in door pull aesthetics
Aesthetic innovations in door pull design are transforming how you approach product development. Modern trends emphasize simplicity and elegance, focusing on clean lines and minimalistic shapes. This approach creates a sophisticated look that appeals to contemporary tastes. You can incorporate these elements into your designs to offer products that align with current market trends.
Comparative Data:
- Traditional mortice door knobs match conventional interiors, while modern mortice door knobs are used in contemporary contexts with a glass or smooth glossy finish.
- Embracing modern elegance focuses on simplicity, clean lines, and minimalistic shapes, while concealed door hardware emphasizes a clean and streamlined look with hidden hinges, locks, and handles.
Examples of unique and modern designs
Examples of unique and modern designs showcase the potential of aesthetic innovations. Some designs feature sleek, glossy finishes that add a touch of luxury to any space. Others incorporate hidden mechanisms, creating a seamless and streamlined appearance. These examples highlight how you can use design flexibility to create door pulls that are both functional and visually appealing.
By embracing these trends, you can enhance your product offerings and meet the evolving expectations of consumers in the Door Pull Injection Molding industry.
Sustainability in Door Pull Injection Molding
In the realm of Door Pull Injection Molding, sustainability has become a pivotal focus. As you navigate this industry, understanding the shift towards eco-friendly materials and energy-efficient processes is essential for aligning with modern environmental standards.
Eco-friendly Materials
The shift towards sustainable materials in manufacturing
Manufacturers are increasingly turning to sustainable materials to reduce their environmental footprint. You can explore biodegradable and renewable options like PLA, PHA, and Bio-PET. These materials not only minimize waste but also offer a viable alternative to traditional plastics. By integrating these eco-friendly materials, you contribute to a more sustainable manufacturing process.
Survey Results:
- Innovative sustainable and bio-based plastic materials: PLA, PHA, and Bio-PET are examples of biodegradable and renewable materials used in injection molding to reduce environmental impact.
This shift reflects a broader trend in the industry, where sustainability is no longer optional but a necessity.
Case studies of eco-friendly door pull projects
Several companies have successfully implemented eco-friendly materials in their door pull projects. For instance, an automotive manufacturer adopted recycled plastics to produce door components, significantly reducing their carbon footprint. Another company utilized bio-based materials to create door pulls that are both durable and environmentally friendly. These case studies demonstrate the practical benefits and feasibility of using sustainable materials in manufacturing.
Energy-efficient Processes
Techniques to reduce energy consumption in production
Reducing energy consumption is a critical aspect of sustainable manufacturing. You can implement various techniques to achieve this goal. For example, using energy-efficient machinery and advanced cooling systems can significantly lower energy usage. Additionally, optimizing production schedules and processes helps minimize waste and improve overall efficiency.
Survey Results:
- Focus on sustainability in manufacturing: Integration of eco-friendly materials and practices, lightweight components, and energy-efficient processes in injection molding.
By adopting these techniques, you not only reduce costs but also contribute to a more sustainable production environment.
Benefits of adopting energy-efficient practices
Embracing energy-efficient practices offers numerous benefits. You can achieve cost savings through reduced energy bills and lower maintenance expenses. Moreover, these practices enhance your company’s reputation as an environmentally responsible manufacturer. By prioritizing energy efficiency, you position yourself as a leader in sustainable manufacturing, meeting the growing demand for eco-friendly products.
Survey Results:
- Adapting injection molding to meet sustainability demands: Use of recycled and bio-based plastics, energy-efficient machinery, and advanced cooling systems to reduce environmental impact.
Incorporating these sustainable practices into your Door Pull Injection Molding operations not only benefits the environment but also strengthens your competitive edge in the market.
Automation in Door Pull Injection Molding
Automation is transforming the landscape of door pull injection molding. By integrating advanced technologies, you can enhance production speed, improve quality, and reduce costs. This section explores how robotics and automated quality control are revolutionizing the industry.
Robotics in Injection Molding
The impact of robotics on production speed and quality
Robotics plays a crucial role in boosting production speed and quality in injection molding. By automating repetitive tasks, you can significantly increase efficiency. Robots handle tasks like part extraction and assembly with precision, reducing the likelihood of human error. This leads to consistent product quality and faster production cycles.
Industry Insight: “Modern assembly lines are increasingly equipped with robotic systems that handle tasks such as part extraction, quality inspection, and packaging, enhancing efficiency and reducing labor costs.”
By adopting robotics, you can streamline operations and focus on higher-value tasks, ultimately improving your bottom line.
Examples of robotic systems in use
Several companies have successfully implemented robotic systems in their injection molding processes. For instance, some manufacturers use robotic arms for part removal and inspection. These systems ensure that each component meets quality standards before moving to the next stage of production.
In another example, automated packaging systems sort and package finished products, reducing manual labor and increasing throughput. These examples demonstrate how robotics can optimize your production line and enhance overall efficiency.
Automated Quality Control
How automation is improving quality assurance
Automated quality control systems are revolutionizing how you ensure product quality. These systems use sensors and cameras to inspect each component in real-time. By identifying defects early, you can prevent faulty products from reaching customers. This proactive approach reduces waste and enhances customer satisfaction.
Industry Insight: “Automation in injection molding generates data and analytics, which will allow users to identify loopholes, and make better manufacturing decisions.”
With automated quality control, you can maintain high standards and build trust with your customers.
Case studies of successful automation implementations
Several companies have reaped the benefits of automated quality control. For example, a leading manufacturer integrated sensors into their production line to monitor product dimensions. This system automatically adjusts settings to maintain consistency, resulting in fewer defects and higher customer satisfaction.
Another company used machine learning algorithms to analyze production data and predict maintenance needs. This approach minimized downtime and improved overall efficiency. These case studies highlight the tangible benefits of automation, encouraging you to explore these technologies for your operations.
By embracing automation in door pull injection molding, you can enhance productivity, improve quality, and stay competitive in a rapidly evolving industry.
In the dynamic world of door pull injection molding, staying informed about emerging trends is essential. These trends, from material innovations to technological advancements, are reshaping industries like automotive and plastics. By embracing these changes, you can enhance product quality and sustainability. The integration of automation and smart technologies boosts efficiency and precision. As you adopt these innovations, you position yourself for success in a competitive market. Understanding these trends ensures you remain at the forefront of industry developments, meeting modern demands and driving future growth.