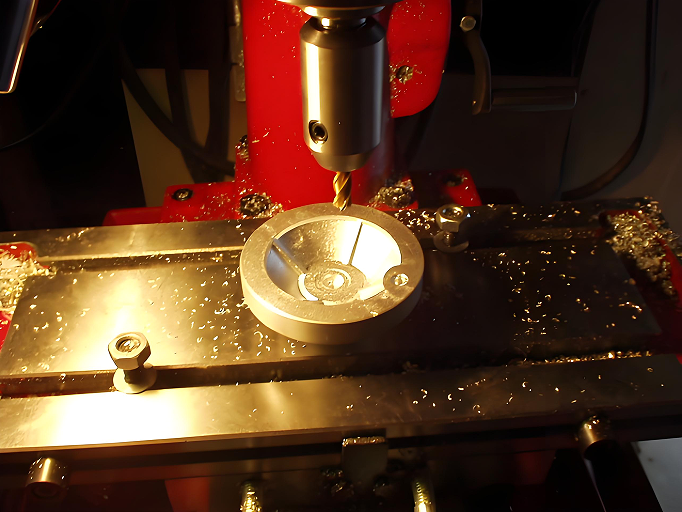
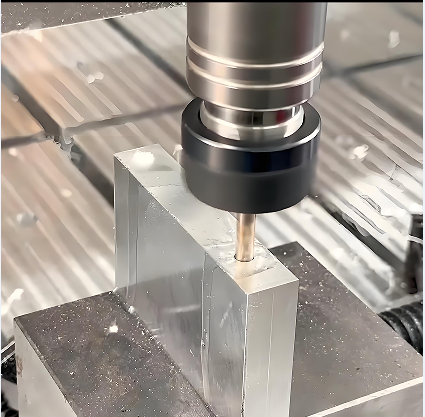
Choosing the right manufacturing process for custom metal parts is crucial. You need to consider factors like precision, volume, and cost. CNC machining offers unmatched precision and flexibility, making it ideal for small runs of complex parts. On the other hand, metal casting excels in high-volume production due to its cost-effectiveness and speed. Each method has its strengths and limitations. Your specific needs will determine which process suits you best. Understanding these differences helps you make informed decisions, ensuring your parts meet the desired specifications and quality.
CNC Machining for Custom Metal Parts
CNC Machining Operations
CNC machining stands as a versatile manufacturing process that allows you to create custom metal parts with remarkable precision. This process involves the use of computer-controlled machines to shape metal into desired forms. You can achieve intricate designs and complex geometries that might be challenging with other methods. CNC machines operate by following programmed instructions, ensuring each part meets exact specifications. This precision makes CNC machining ideal for producing highly accurate parts with tight tolerances, especially when dealing with small or niche components.
Benefits of CNC Machining
When you choose CNC machining for your custom metal parts, you gain several advantages:
- High Precision: CNC machining excels in delivering parts with exceptional accuracy. This is crucial when you need parts that fit perfectly into larger assemblies.
- Complex Designs: The ability to produce intricate and complex designs sets CNC machining apart. You can create parts with detailed features that other processes might struggle to replicate.
- Durability: Parts produced through CNC machining are known for their robustness. This durability ensures that your components withstand demanding applications.
- Material Versatility: CNC machining works with a wide range of materials, allowing you to select the best option for your specific needs.
- Efficiency: For medium to high production runs, CNC machining offers excellent efficiency, making it a cost-effective choice for precise parts.
Limitations of CNC Machining
Despite its many benefits, CNC machining does have some limitations:
- Cost for Low Volume: For small production runs, the initial setup costs can be high. This might not be the most economical choice if you only need a few parts.
- Material Waste: CNC machining involves cutting away material, which can lead to waste. This might not be ideal if you're working with expensive materials.
- Complexity in Setup: Setting up CNC machines requires skilled operators and precise programming. This complexity can increase lead times for new projects.
By understanding these aspects of CNC machining, you can better determine if it's the right process for your custom metal parts. Whether you prioritize precision, complexity, or durability, CNC machining offers a reliable solution for many manufacturing needs.
Metal Casting for Custom Metal Parts
Metal Casting Process
Metal casting is a formative manufacturing process that involves creating a mold to shape your custom metal parts. You pour molten metal into this mold, allowing it to cool and solidify completely. This method can produce intricate and complex parts of various sizes. Different techniques, such as die casting, are tailored to meet specific design and production requirements. Die casting, for instance, uses high pressure to inject molten metal into a steel mold, which can be reused multiple times. This process is particularly effective for creating geometrically complex parts.
Benefits of Metal Casting
When you opt for metal casting, you gain several advantages:
- Design Flexibility: Metal casting allows you to create intricate shapes and complex geometries that might be challenging with other methods.
- Cost-Effectiveness: For high-volume production, metal casting proves to be cost-effective due to its ability to reuse molds and produce parts quickly.
- Material Versatility: You can use a wide range of metals in casting, giving you the flexibility to choose the best material for your application.
- Production Efficiency: Metal casting excels in producing large quantities of parts efficiently, making it ideal for industries requiring mass production.
Limitations of Metal Casting
Despite its benefits, metal casting has some limitations:
- Initial Setup Costs: Creating molds can be expensive, especially for complex designs. This might not be economical for low-volume production.
- Surface Finish: Parts produced through casting may require additional finishing processes to achieve the desired surface quality.
- Dimensional Accuracy: While casting can produce complex shapes, achieving tight tolerances can be challenging compared to CNC machining.
By understanding these aspects of metal casting, you can better assess if it's the right process for your custom metal parts. Whether you prioritize design flexibility, cost-effectiveness, or production efficiency, metal casting offers a viable solution for many manufacturing needs.
Direct Comparison of CNC Machining and Metal Casting
Complexity and Design Flexibility
When it comes to creating custom metal parts, both CNC machining and metal casting offer unique advantages in terms of complexity and design flexibility. CNC machining excels in producing parts with intricate details and tight tolerances. You can achieve highly precise and repeatable designs, making it ideal for components that require exact specifications. This process allows for easy modifications, enabling you to test and refine prototypes without the need to create new molds.
On the other hand, metal casting shines in its ability to produce complex shapes with thin walls and intricate details. It allows for the creation of hollow parts and internal cavities that might be challenging to achieve through machining. While casting may not match the precision of CNC machining, it offers significant design flexibility, especially for large-scale production.
Cost and Production Volume
Cost considerations play a crucial role in choosing between CNC machining and metal casting for your custom metal parts. CNC machining tends to be more expensive for low-volume production due to the initial setup costs and material waste. However, it becomes cost-effective for medium to high production runs, where precision and complexity are paramount.
In contrast, metal casting proves to be more economical for high-volume production. The ability to reuse molds reduces costs significantly, making it a preferred choice for mass production. While the initial mold creation can be costly, the per-unit cost decreases as production volume increases. This makes casting a viable option for industries requiring large quantities of parts quickly.
Material Compatibility
Material compatibility is another critical factor when deciding between CNC machining and metal casting. CNC machining offers a wide range of material options, allowing you to select the best material for your specific needs. Whether you require metals like aluminum, steel, or titanium, CNC machining can accommodate your requirements.
Metal casting, while versatile, has more limited material options compared to CNC machining. It works well with metals like aluminum, zinc, and magnesium, but may not be suitable for all materials. Despite this limitation, casting remains a reliable choice for producing durable and solid parts.
By understanding these differences, you can make informed decisions about which process best suits your custom metal parts. Whether you prioritize precision, cost-effectiveness, or material compatibility, both CNC machining and metal casting offer valuable solutions for various manufacturing needs.
Selecting the Right Process for Specific Applications
Choosing between CNC machining and metal casting for your custom metal parts requires careful consideration of several factors. Each method offers unique benefits and limitations, making it essential to align your choice with your specific application needs.
Factors to Consider
-
Production Volume: If you need a large number of parts, metal casting often proves more cost-effective. The ability to reuse molds reduces costs significantly in high-volume production. However, for smaller batches, CNC machining might be more economical despite its higher initial setup costs.
-
Precision and Tolerances: CNC machining excels in delivering parts with tight tolerances and high precision. This makes it ideal for applications where exact specifications are crucial. Metal casting, while capable of producing complex shapes, may not achieve the same level of precision as CNC machining.
-
Material Requirements: Consider the materials you plan to use. CNC machining offers a broader range of material options, accommodating metals like aluminum, steel, and titanium. Metal casting works well with metals such as aluminum, zinc, and magnesium but may not suit all materials.
-
Design Complexity: For intricate designs with detailed features, CNC machining provides unmatched flexibility. You can easily modify designs without creating new molds. Metal casting, however, allows for the creation of complex shapes with internal cavities, which might be challenging to achieve through machining.
-
Cost Considerations: Evaluate the overall cost implications. While CNC machining might have higher upfront costs, it becomes cost-effective for medium to high production runs. Metal casting offers lower per-unit costs in mass production, making it suitable for industries requiring large quantities of parts quickly.
Industry-Specific Recommendations
-
Automotive Industry: For automotive components requiring high precision and strength, CNC machining is often preferred. It ensures parts meet stringent quality standards and fit seamlessly into larger assemblies.
-
Aerospace Industry: Aerospace applications demand parts with exceptional accuracy and durability. CNC machining provides the precision needed for critical components, ensuring safety and performance.
-
Consumer Electronics: In consumer electronics, where design complexity and lightweight structures are essential, metal casting can be advantageous. It allows for the production of intricate shapes efficiently.
-
Industrial Equipment: For industrial equipment requiring robust and durable parts, metal casting offers a cost-effective solution for mass production. It provides the necessary strength and consistency for demanding applications.
By understanding these factors and industry-specific recommendations, you can make informed decisions about the most suitable manufacturing process for your custom metal parts. Whether you prioritize precision, cost-effectiveness, or material compatibility, aligning your choice with your application needs ensures optimal results.
Choosing between CNC machining and metal casting requires understanding their key differences. CNC machining offers high precision and flexibility, making it ideal for intricate designs and small production runs. Metal casting, however, excels in high-volume production with cost-effectiveness and speed. To select the right process, consider factors like production volume, precision needs, and material compatibility. Consulting with experts can provide tailored advice, ensuring your manufacturing process aligns with your specific project requirements. By aligning your production needs with the appropriate method, you ensure optimal results for your custom metal parts.